注塑模具注塑加工脱模困难什么原因造成和解决方案?
在注塑模具注塑加工试模的时候,经常会发生脱模困难的现象。总结如下:
注塑模具注塑加工脱模困难的原因包括很多方面:
1、水路的设计;
2、模具内部有凹槽;
3、前后模的脱模情况;
4、模具光洁度不高;
5、脱模斜度不足;
6、斜顶与顶针的定出是否一致。
脱模斜度不足是造成脱模困难的一个重要原因之一。因此在进行
注塑模具注塑加工制品设计的时候,要在图面上标明斜度,通常是在1-2度之间,特殊的场合允许为0.5以上。在操作的时候,为了顺利使塑胶制品脱离模具,会使用含有硅油的脱模剂,但是只能使用一点点。喷涂太厚想擦去就非常的难。同时还会导致打印标记第二次加工变得不好,一旦涂布在模具上脱模剂就会附在塑胶制品上想擦去那就非常困难了。要注意射出压力不能太高,塑胶制品同注塑模具之间太紧密贴紧,脱模就会变得非常困难。
塑胶注塑件脱模困难在我们注塑生产过程中经常遇到,脱模不良对于注塑产品的质量有着非常大的影响,轻度脱模不良可能造成制品表面划伤或花纹;严重的脱模不良会导致产品翘曲变形甚至破裂伤损。所以解决注塑模具注塑加工脱模不良问题影响着最终注塑产品的质量。
在塑件注塑成型后,塑件从模具型腔中脱出,无论是采用单一的或多元件的顶出机构,其脱模工作一般都是一次性完成的。但有时由于塑件的特殊形状或生产自动化的需要,在一次脱模工作完成后,塑胶注塑件仍难以从型腔中取出或不能自动脱落,此时就须再增加一次脱模动作才能使塑件脱落。脱模困难主要是因为浇口或塑件紧缩在模具内。
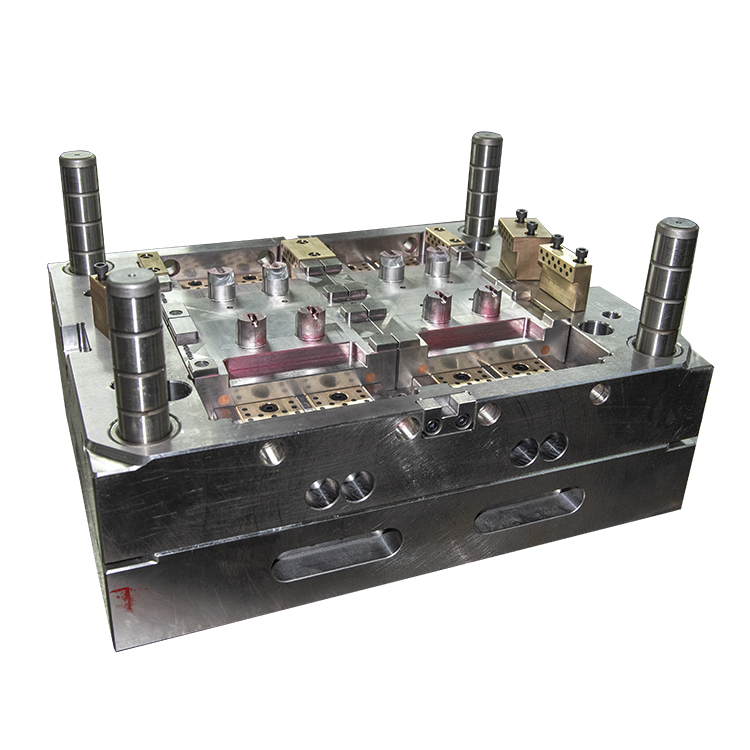
其中的解决方案从以下几方面进行考虑:
一、设备方面:顶出力不够、顶程不够。
顶出力是注塑设备用于脱模的力度控制,对于不同重要级的注塑机台,最大顶出力各不相 同。理想的注塑过程机台预设顶出力基本足够,但不排除在注塑件大于最大注塑范围或注塑件结构过于复杂,模内抓力过大的情况,综合考虑这些问题有利于分析顶出力的适合情况。
二、注塑模具注塑加工模具方面
1、脱模结构不合理或位置不当;
2、脱模斜度不够;
3、模温过高或通气不良;
4、浇道壁或型腔表面粗糙;
5、喷嘴与模具进料口吻合不服帖或喷嘴直径大于进料口直径。
三、注塑模具注塑加工工艺方面
1、机筒温度太高或注射量太多。模温太高的时候,腔内熔料冷却未到位,体积没有恢复到预设大小,从而引发脱不了模的情况;
2、注射压力太高或保压及冷却时间长。注塑温度包括机筒温度、喷嘴温度等,温度过高熔料进入型腔内无法在预定时间冷却成型,同样影响脱模效果;
3、注射量过多。注射量超过型腔容量,就是我们常说的胀模了,注入过多的熔料在压力释放时就会扩张,从而胀紧在模具上无法脱下,调整注射量即可以解决;
4、注塑周期不当。注塑时如果注射压力过大、保压时间或冷却时间过长时,也有造成脱模困难的隐患,完全冷却的制品也不利于脱模,注塑周期要适当即可。
四、原料方面:润滑剂不足。
传统的塑料模塑件的脱模方法大致分为为顶、推、抽、旋四种。
现在有一种较新脱模技术可以轻松解决塑胶脱模问题。在塑胶模具行业中,特别是需要用各种树脂化合物进行高度复杂的设计,外观高光泽精加工时 ,存在很多不可解决的问题。
纳米脱模涂层可以在塑胶模具表面,甚至在塑胶模具的插件表面形成涂层,可明显的降低这些表面的摩擦系数,不必使用传统的脱模剂即可达到高度光泽的加工面. 即使在所使用的设计及塑料化合物使得机器/工具维修停产期较长,以致于生产产量低,经济上不可行的临界情况下,纳米脱模涂层也可延长不间断生产时间,明显降低机器/工具维护停产期. 使塑胶模具生产发挥较大的效率和作用,减少浪费。纳米脱模涂层不仅改善了塑胶模具表面的光滑度、精确度,还大幅度提高了塑胶模具制造工业的生产率!
东莞世邦塑胶是一家多年专业从事精密模具设计制造及精密注塑制品生产集团企业,公司专注于为好的品牌提供从产品设计、精密模具制造、注塑成型与组装、售后服务为一体整套解决方案,产品广泛应用于家用家电器外壳配壳配件、医疗医用器械注塑配件、化妆品包装注塑件等领域,欢迎来电咨询13332683013(微信同号)